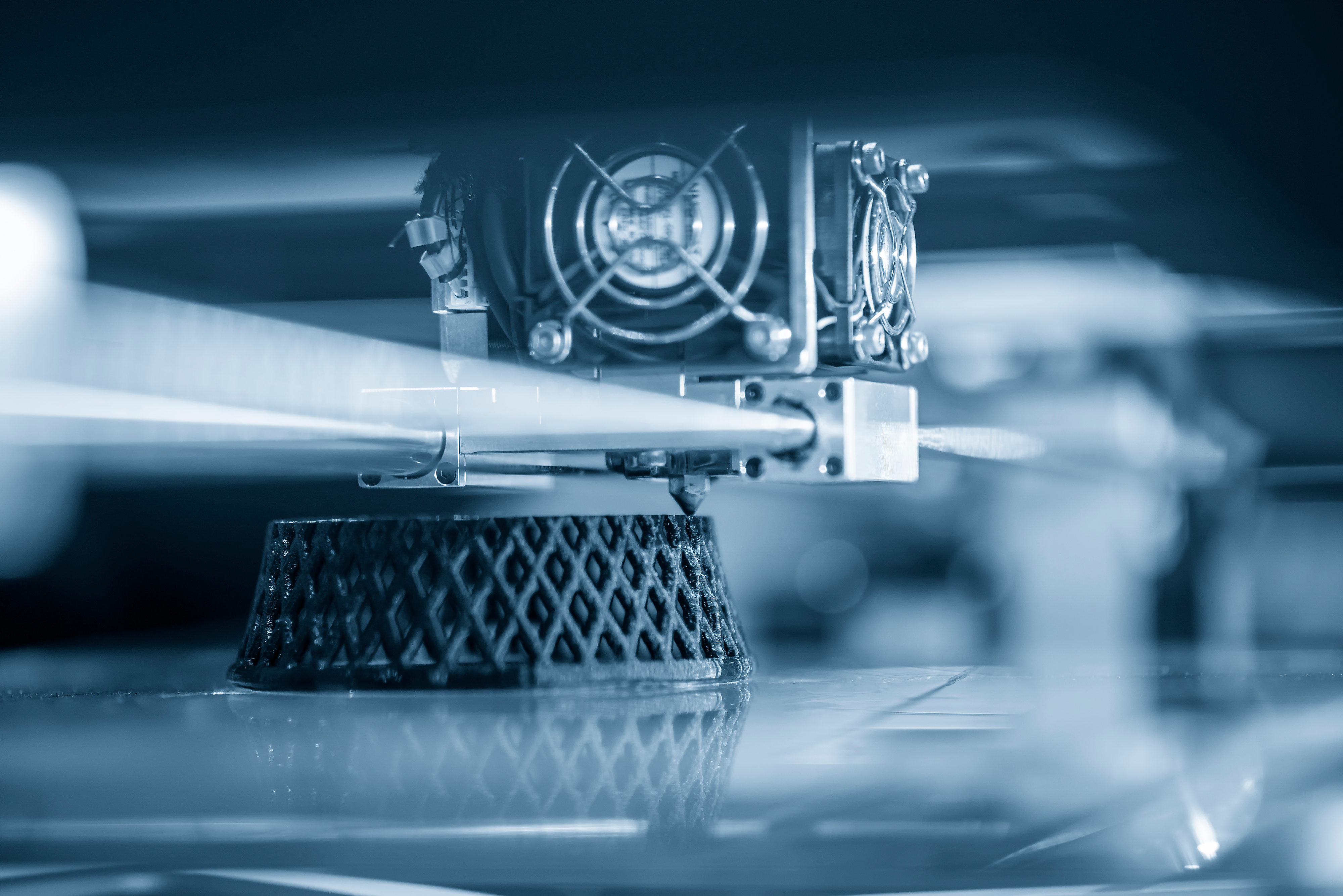
W świecie, gdzie innowacja i technologia kształtują przyszłość, Finnotech wyróżnia się jako pionier w dziedzinie druku 3D. Od 2014 roku, z pasją i zaangażowaniem przekształca wizje w rzeczywistość, wykorzystując zaawansowane technologie modelowania przestrzennego. W wywiadzie z Prezesem Zarządu, Łukaszem Mikłowski oraz dr hab. Michałem Sobotą dowiemy się o drodze firmy do stania się liderem innowacyjnego sektora gospodarki. Zapytamy o wyzwania oraz aktualne projekty, które napędzają spółkę do ciągłego rozwoju i poszukiwania nowych horyzontów.
Czy mógłby Pan przybliżyć historię firmy na rynku, rozpoczynając od roku jej założenia w 2014 roku?
Łukasz Mikłowski: Spółka została założona w 2014 roku i od tego czasu nieustannie rozwija się w dziedzinie druku 3D. Początkowo, gdy technologia ta była jeszcze niszowa, skupialiśmy się na produkcji dla zewnętrznych klientów. Z biegiem lat nasza pasja i ambicja do rozwoju tej technologii tylko wzrosła, co pozwoliło nam osiągnąć wiele kamieni milowych. Od 2014 roku formalnie zaangażowałem się w działalność jako prezes. Moje wcześniejsze doświadczenie w branży sięga 2012 roku, kiedy to pracowałem nad konfekcją materiałów dla międzynarodowego giganta, we współpracy z brytyjską spółką świadczącą podobne usługi. W tym czasie zdobywałem wiedzę na temat branży druku. Wracając do firmy jednym z naszych ważniejszych osiągnięć było stworzenie własnego parku maszynowego oraz marki F3DFilament, która dystrybuuje materiały do druku technologii FDM na całą Europę.
Jakie istotne zmiany zaobserwowano w ciągu ostatniej dekady w kontekście działalności firmy?
Ł. M.: W ciągu ostatniej dekady zaobserwowano znaczący rozwój technologiczny w obszarze druku 3D, który stał się bardziej dostępny nie tylko dla dużych korporacji, ale również dla przeciętnych użytkowników. Ten postęp technologiczny dotyczy wielu gałęzi przemysłu, biznesu, medycyny i sztuki. Firmy, takie jak nasza działają z przedsiębiorstwami, które zajmują się różnorodnymi dziedzinami, od budownictwa po sztukę odtworzeniową. Na przykład, nasza współpraca ze Stokłosa z Bytomia zaowocowała stworzeniem narzędzia do odtworzenia specyficznego tynku elewacyjnego na obiekcie zabytkowym. Dzięki naszym zdolnościom w druku 3D mogliśmy precyzyjnie odtworzyć teksturę tego materiału, co było niemożliwe przy użyciu tradycyjnych metod. Nasze działania widoczne są również na katedrze Chrystusa Króla w Katowicach, gdzie pomagamy w produkcji form pod rzeźby betonowe, co znacznie redukuje ich wagę i ułatwia montaż. Druk 3D znajduje zastosowanie również w innych branżach, takich jak przemysł samochodowy czy lotniczy, a także w medycynie, gdzie wykorzystuje się go do produkcji aparatów ortodontycznych. To tylko kilka przykładów, które pokazują, jak technologia ta stała się powszechnie wykorzystywana i wpływa na różnorodne aspekty życia codziennego.
Podsumowując, jakie kluczowe zmiany zaobserwowali Państwo, zwłaszcza w kontekście ułatwionego i bardziej dostępnego dostępu do rozwiązań technologicznych, które wcześniej były również bardzo drogie?
Ł. M.: Zmiany w dostępie do rozwiązań technologicznych, zwłaszcza w zakresie druku 3D, były znaczące w ostatnich latach. Wcześniejsze patenty, które były kontrolowane przez duże podmioty od lat 80. XX wieku, stopniowo wygasły w latach 2012-2015, otwierając pole do działania dla większej liczby firm na całym świecie. Pierwsze komercyjne maszyny do druku 3D były dość ograniczone, oferując możliwość druku zaledwie z kilku materiałów, głównie PLA i ABS. Ich cena, nawet w promocji, była stosunkowo wysoka w porównaniu do obecnych standardów, oscylując wokół 3,5 tysiąca funtów. Jednak obecnie, za podobną cenę, możemy nabyć znacznie bardziej zaawansowane maszyny, oferujące większe pole robocze i zdolność do druku z większej liczby materiałów, nawet do 10-15 różnych rodzajów. To zdecydowanie ułatwiło i zdemokratyzowało dostęp, umożliwiając coraz większej liczbie firm na całym świecie eksperymentowanie, modyfikowanie i wykorzystywanie tej innowacyjnej technologii do różnych celów, od przemysłu po medycynę i sztukę.
Do jakich klientów głównie jest skierowana Państwa oferta?
Ł. M.: Nasza oferta jest skierowana głównie do osób indywidualnych oraz instytucjonalnych, takich jak uczelnie naukowe, zakłady technologiczne oraz produkcyjne i prototypowe. Współpracujemy również z firmami budowlanymi oraz zespołami stenografów, przy czym nasze działania obejmują zarówno odtwarzanie, jak i budowę całych konstrukcji, czasem nawet z okresów historycznych, które obecnie są trudno dostępne na rynku, jak na przykład elementy związane z czasami II wojny światowej, które odtwarzaliśmy.
Czym wyróżnia się Państwa firma w porównaniu do konkurencji?
Ł. M.: Na rynku istnieje obecnie pięć znaczących firm, które konkurują ze sobą. Jeśli chodzi o produkcję filamentu, pojawiają się również mniejsze podmioty, które czasem znikają, czasem łączą się z innymi. Konkurencja na rynku jest zatem dość zróżnicowana, a każda firma stara się wyróżnić poprzez innowacyjność, jakość produktów i obsługę klienta. Naszym głównym wyróżnikiem na rynku jest jedno z najszerszych portfolio dostępnych materiałów i mieszanek tworzyw sztucznych. Od zawsze naszą cechą charakterystyczną było posiadanie szerokiej gamy produktów – gdy konkurencja miała w ofercie około 12 materiałów, my dysponowaliśmy 26-cioma. Dodatkowo, oferujemy także bogactwo kolorów w około 40 różnych odcieniach. Ta różnorodność produktów umożliwia nam sprostanie różnym potrzebom i oczekiwaniom klientów, co stanowi nasz kluczowy atut na rynku.
Chciałbym poruszyć kwestię projektu, który Państwo ostatnio realizowaliście, który jak się zdaje, został już zakończony. Mowa o projekcie dotyczącym opracowania bioresorbowalnego filamentu, który ma zwiększyć funkcjonalność technologii druku 3D w zastosowaniach biomedycznych. Czy mógłby Pan Doktor podzielić się informacji na temat przebiegu tej inwestycji oraz jakie wnioski udało się wyciągnąć?
Dr hab. Michał Sobota: Projekt zakończył się sukcesem.Przebieg realizacji był wymagający, ale dzięki elastyczności naszego zespołu oraz otwartości Prezesa Mikłowskiego na nowe rozwiązania, udało nam się osiągnąć zamierzone cele. Materiał wykorzystywany do produkcji filamentu, opracowany już kilkadziesiąt lat temu, wyróżnia się innowacyjnym podejściem opartym na cyrkonie, co sprawia, że jest mniej toksyczny niż obecnie stosowane inicjatory. Nasze badania nad tym materiałem stanowią istotny wkład w rozwój nowych technologii. Pomimo ograniczeń finansowych, nasz zespół jest gotowy do wyzwań i planuje dalszy rozwój w tej dziedzinie. Mamy nadzieję, że nasze działania przyczynią się do promocji Polski jako centrum innowacyjnych rozwiązań w dziedzinie technologii medycznych.
Mógłby Pan wyjaśnić zrozumiale dla osoby niezorientowanej w temacie, w jakich konkretnych obszarach medycyny głównie znajduje zastosowanie opracowywany przez Państwa filament?
M.S.: Materiał, nad którym pracujemy znajduje zastosowanie głównie w obszarze medycyny, ze względu na jego biozgodność oraz zdolność do promowania proliferacji komórkowej. Doskonale sprawdza się jako składnik do hodowli tkankowej oraz w tkankach kostnych, gdzie może być wykorzystywany jako wzmocnienie ortopedyczne. W przypadku protetyki ortopedycznej dla dzieci, może być stosowany do produkcji płytek chirurgicznych oraz pinów mocujących. Jego zakres zastosowań obejmuje wszelkie obszary, gdzie materiał ten ma być zastąpiony później przez tkankę. Warto jednak zachować ostrożność przy zastosowaniu w kościach długich u dorosłych osób, ze względu na obciążenia, jakie muszą one wytrzymać. Natomiast w przypadku tkanki pozostałej, materiał ten może być stosowany we wszystkich miejscach, gdzie jest to możliwe, np. jako rusztowanie do hodowli komórkowej. Jednakże, w przypadku implantów kostnych, istnieją pewne ograniczenia wynikające zarówno z własności mechanicznych, jak i medycznych. Mimo to, materiał ten posiada duży potencjał do zastosowania, szczególnie tam, gdzie wymagane jest jednorazowe wszczepienie bez konieczności usuwania elementu.
Jakie są Państwa plany dotyczące komercjalizacji tego rozwiązania?
M.S.: Planujemy wprowadzenie rozwiązania na rynek poprzez początkową penetrację sektora weterynaryjnego, co stanowi zazwyczaj pierwszy etap przed przeniesieniem się na rynek ludzki. Nasz proces rozwoju zakłada dalsze kroki, o ile finanse oraz zainteresowanie rynku nadal pozostanie. Istnieje szansa, że po udanych badaniach klinicznych nasze produkty zostaną wdrożone do szpitali, z którymi już nawiązaliśmy współpracę. Działamy również z instytucjami badawczymi oraz rozwojowymi zainteresowanymi weterynarią, co pozwoli nam ocenić zainteresowanie rynku i przewidzieć jego reakcję. Oczywiście, istnieje ryzyko pojawienia się konkurencji, zwłaszcza z Chin, jednak nasze opatentowane rozwiązanie posiada unikalne cechy, które wyróżniają je na tle innych produktów.
Jak Pan jako Prezes, ocenia panujący trend rozwoju technologii druku 3D w Polsce i w skali globalnej? Jakie są prognozy dotyczące przyszłego wzrostu tego sektora?
Ł. M.: Rozwój druku 3D jest dynamiczny zarówno w Polsce, jak i na świecie. Obserwujemy coraz większą penetrację tych technologii w różnych sektorach, co przekłada się na coraz szersze zastosowania. Nasza firma także aktywnie uczestniczy w tym procesie. Planujemy wprowadzić kilka istotnych zmian, które zostaną oficjalnie ogłoszone w listopadzie tego roku. Dodatkowo, zamierzamy publikować wyniki naszych badań oraz uczestniczyć w konferencjach, aby przedstawić nasze osiągnięcia. Nasze działania nie ograniczają się jedynie do medycyny, ale także do innych obszarów, gdzie poszerzamy nasze portfolio materiałowe. W związku z tym, planujemy zakupić kilka nowych linii technologicznych, aby zoptymalizować proces produkcji oraz zwiększyć różnorodność oferowanych materiałów, które wymagają bardziej zaawansowanych urządzeń. Dążymy do utrzymania konkurencyjności i atrakcyjności naszych produktów na rynku.
Bartosz Parchoniuk
